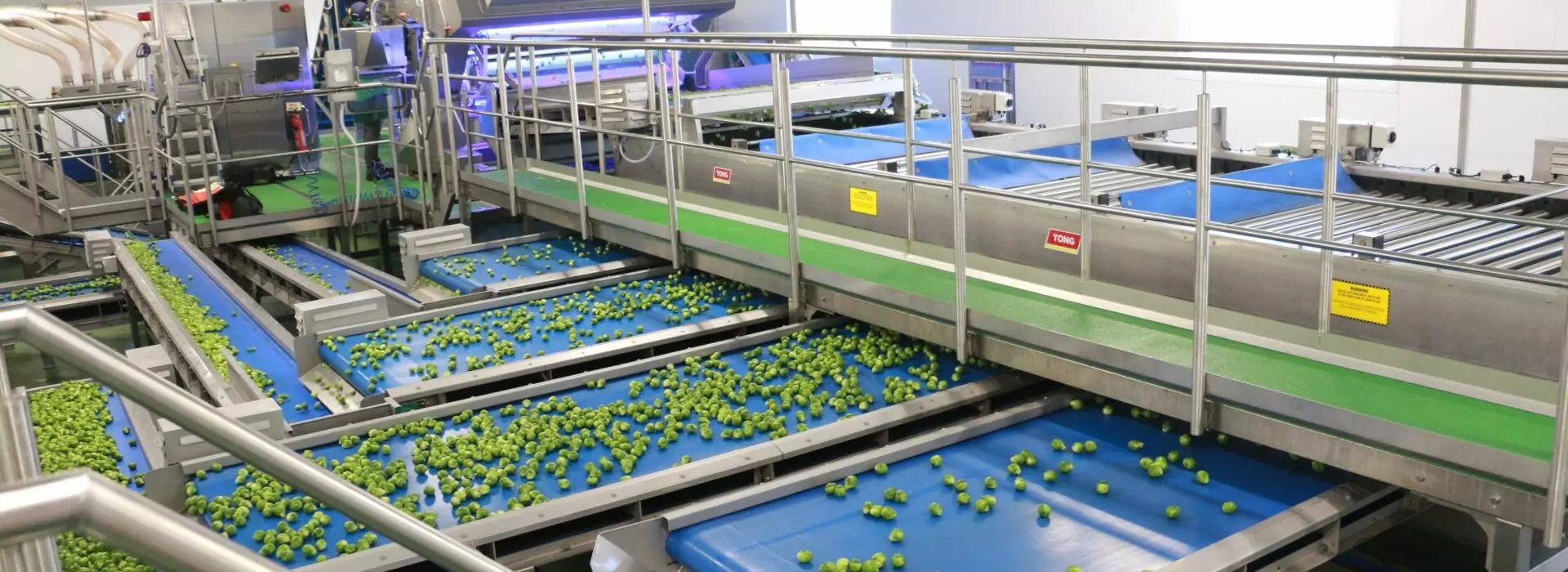
With a passion for producing the freshest vegetables of the very best quality, TH Clements & Son Ltd based in Boston, Lincolnshire, chose Tong Engineering to design a new Brussels sprouts grading and sorting facility, to increase the throughput and efficiency of its Brussels sprouts handling operations.
TH Clements harvest over 20 different varieties of Brussels sprouts over 1000 acres across Lincolnshire. Harvesting takes placed between August and March, reaching a peak throughout the festive season. Supplying to some the UK’s major supermarkets, the company produces high quality Brussels sprouts ranging from whole loose product to bagged, peeled and sliced, distributing them across the UK.
In line with the company’s ongoing programme of growth and investment, TH Clements looked to Tong Engineering when the time came to update their existing Brussels sprouts grading and processing operations in order to significantly expand their capabilities.
“Our original Brussels sprouts grading system involved a great deal of manual sorting, and subsequently labour requirements,” explains Graham Neal, Project Manager at TH Clements. “Our throughput capabilities were increasingly limited, and as new and existing contracts developed, we were finding it difficult to achieve the wide range of grading sizes that were demanded by our customers. Not only that, as the original system had been updated over the years, the layout was becoming increasingly inefficient, making equipment difficult to clean and maintain effectively.”
“With this in mind, the decision was made to replace the original system with a new custom-built grading and sorting line from Tong, which incorporated the latest technology for maximum efficiency and productivity,” said Graham. “We needed a new facility that would improve the quality of the grading process, increase throughput capacity and reduce labour requirements. Tong designed a complete Brussels sprout intake and grading system that meets all our grade size requirements and incorporates the new Veryx digital sorter from Key Technology for exceptionally fast and consistent defect sorting.”
The new handling facility gently handles TH Clements’ Brussels Sprouts from receiving the harvested sprouts in boxes to cleaning, drying, grading and defect sorting crop prior to reaching the packing area. The new stainless steel line starts with a Tong box rotator at the infeed, which gently tips crop into a Tong hopper that ensures an even flow of crop over a debris removing screen and overhead crop drying unit. A new Tong Lift Roller Grader size grades the Brussels sprouts to a variety of pre-set grade bands to suit customer requirements, which can be easily adjusted at the touch of a button with Tong’s advanced Auto-Touch HMI controls.
Defect sorting with the new Veryx sorter from Key Technology means that TH Clements Brussels sprout crop is sorted with increased accuracy and consistency. The innovative sensor technology of the Veryx means that it is the first sorter to deliver total product inspection, ensuring sustained 360 degree vision of crop as it passes through the sorting unit. The Veryx, which works upon a simple accept and reject system, operates upon a range smart features such as auto-learning, self-adjustment algorithms, predictive system diagnostics and smart alarms which allow the sorter to operate virtually unattended during normal production.
“Our new Brussels sprouts facility has exceeded our expectations,” said Graham. “It is so much more productive. We no longer have to perform screen changes to meet all the grade sizes required. Now we simply make our grade selections on the touch screen and the machine adjusts automatically. The diagnostics features on the line mean that any downtime is minimal, and the whole line is much easier to maintain and clean. The consistency, performance and capacity of the Veryx has transformed our throughput capabilities.”
Nick Woodcock, Sales Manager at Tong Engineering added “The new Tong line has fully integrated the latest sorting technologies to ensure TH Clements has the capacity to be very flexible and responsive to their customer demand. Throughput and consistency has significantly increased, and with much easier and proactive maintenance, they can be sure their new investment will bring maximum performance for many years to come.”